多头丝锥是一种在同一轴线上具有多个切削刃的丝锥,其结构特点是在丝锥的圆周上均匀分布着多个切削刃,每个切削刃负责加工一部分螺纹。多头丝锥的主要优点是加工效率高,可明显缩短攻丝时间。多头丝锥的加工效率高主要体现在以下几个方面:① 多刃切削:多头丝锥的多个切削刃同时参与切削,每个切削刃的切削负荷减小,可采用更高的切削速度和进给量,从而提高加工效率。② 减少切削行程:由于多头丝锥的每个切削刃只加工一部分螺纹,因此丝锥的切削行程缩短,攻丝时间减少。③ 改善排屑性能:多头丝锥的容屑槽数量增多,排屑空间增大,排屑性能得到改善,可减少切屑堵塞和丝锥折断的风险。多头丝锥的缺点是结构复杂,制造难度大,成本高;对机床的动力和刚性要求较高,否则容易产生振动和噪声。攻丝的进给运动必须与主轴旋转严格同步,否则会导致螺纹乱扣或丝锥折断,数控机床上可通过 G 指令实现同步。东莞TICN丝锥
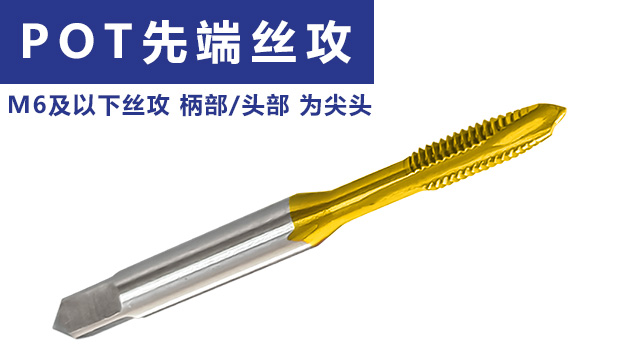
攻丝过程中的振动会导致螺纹表面粗糙度增加、尺寸精度下降、丝锥寿命缩短等问题。因此,控制攻丝过程中的振动是保证螺纹加工质量的关键。攻丝过程中的振动主要由以下原因引起:① 机床刚性不足:机床的刚性不足会导致在攻丝过程中产生振动。解决方法是选择刚性好的机床,或对机床进行加固和改进。② 丝锥夹持不牢固:丝锥夹持不牢固会导致在攻丝过程中丝锥产生晃动,引起振动。解决方法是使用高精度的丝锥夹头,确保丝锥夹持牢固。③ 切削参数不当:切削速度过高、进给量过大或切削深度过深都会导致切削力增大,引起振动。解决方法是调整切削参数,选择合适的切削速度、进给量和切削深度。④ 丝锥几何参数不合理:丝锥的螺旋角、后角等几何参数不合理会导致切削力分布不均匀,引起振动。解决方法是优化丝锥的几何参数,使切削力分布均匀。⑤ 工件材料不均匀:工件材料的硬度、组织等不均匀会导致切削力波动,引起振动。解决方法是对工件材料进行预处理,如退火、调质等,使材料均匀。东莞涂层丝锥机用丝锥适用于机床自动化加工,具有较高的强度和耐磨性,能够在高速切削条件下保持螺纹质量的稳定性。
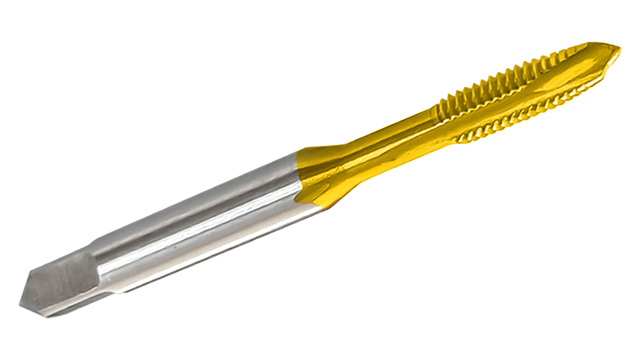
强度高得材料如淬火钢、钛合金、镍基合金等的攻丝是机械加工中的难点之一。这些材料硬度高、强度大、韧性好,攻丝时容易出现丝锥磨损快、折断、螺纹表面质量差等问题。为优化强度高材料的攻丝工艺,可采取以下措施:① 选择合适的丝锥材料:应选用硬质合金、粉末冶金高速钢等高性能材料的丝锥,这些材料具有较高的硬度和耐磨性,能够承受强度高的材料的切削力。② 优化丝锥几何参数:适当增大丝锥的前角和后角,以减小切削力;采用螺旋槽或螺尖设计,改善排屑性能;增加丝锥的倒锥量,减少丝锥与螺纹孔壁的摩擦。③ 合理选择切削参数:降低切削速度,一般为 5~10m/min;减小进给量,一般为 0.5~1.0mm/r;采用较小的切削深度,避免一次切除过多材料。④ 采用合适的冷却润滑方式:使用极压切削油或含有硫、氯等极压添加剂的切削液,提高冷却和润滑效果,减少丝锥磨损。⑤ 预处理材料:对强度高的材料进行适当的预处理,如退火、调质等,降低材料硬度,改善加工性能。⑥ 分步攻丝:对于大直径螺纹或深孔攻丝,可采用分步攻丝的方法,先用较小直径的丝锥预攻,再用标准丝锥进行后续加工,以减小切削力。
当丝锥出现磨损或崩刃时,可通过修磨来恢复其性能。丝锥的修磨工艺包括刃磨切削刃、修磨后刀面和清理容屑槽等。刃磨切削刃是丝锥修磨的关键步骤,需使用对应的丝锥磨床或工具磨床。修磨时,应保证切削刃的锋利度和对称性,避免出现刃口崩裂或钝圆。修磨后刀面可减少丝锥与工件的摩擦,提高丝锥的使用寿命。清理容屑槽可去除切屑和污垢,保证切屑的顺利排出。在丝锥修磨过程中,需注意以下事项:① 修磨前需对丝锥进行清洗和检查,确定磨损部位和程度;② 修磨时需使用合适的砂轮和磨削参数,避免烧伤丝锥材料;③ 修磨后的丝锥需进行尺寸检测和表面质量检查,确保符合要求;④ 对于硬质合金丝锥,修磨后需进行涂层处理,以恢复其原有性能;⑤ 丝锥的修磨次数不宜过多,一般不超过 3 次,否则会影响丝锥的强度和精度。丝锥的修磨需要专业的设备和技术人员,因此在实际生产中,可将磨损的丝锥送回制造商或专业的刀具修磨厂家进行修磨。攻丝过程中的扭矩监测可实时反映加工状态,当扭矩超过设定阈值时,系统可自动报警或停机,防止丝锥损坏。
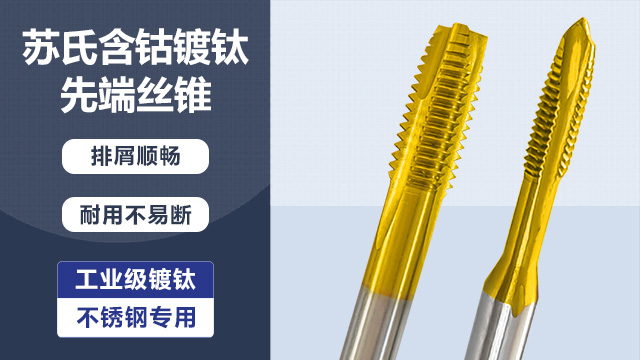
难加工材料如不锈钢、钛合金、高温合金等的攻丝是机械加工中的难点之一。这些材料硬度高、韧性大、导热性差,攻丝时容易出现丝锥磨损快、折断、螺纹表面质量差等问题。为解决这些问题,可采用分步攻丝工艺。分步攻丝工艺是指将螺纹加工分成多个步骤进行,每个步骤使用不同的丝锥或加工参数,逐步完成螺纹加工。分步攻丝工艺的主要优点是可以减小每次切削的切削力和扭矩,降低丝锥的磨损和折断风险,提高螺纹加工质量。分步攻丝工艺通常包括以下几个步骤:① 预钻孔:使用比丝锥直径略小的钻头预钻孔,以确定螺纹的位置和方向。预钻孔的直径应根据材料的特性和丝锥的类型来确定,一般为螺纹小径的 0.9~0.95 倍。② 初攻:使用初攻丝锥进行初次攻丝。初攻丝锥的切削锥长度较长,锥度较小,便于切入材料。初攻时,应采用较低的切削速度和进给量,以减小切削力和扭矩。③ 复攻:使用复攻丝锥进行第二次攻丝。复攻丝锥的切削锥长度较短,锥度较大,用于进一步加工螺纹,提高螺纹的尺寸精度和表面质量。复攻时,可适当提高切削速度和进给量。④ 精攻:对于精度要求较高的螺纹,可使用精攻丝锥进行第三次攻丝。苏氏螺旋丝攻的螺旋槽是经过精密磨削工艺加工,保证了螺旋精度,使得能够在复杂加工条件下发挥出色性能。东莞涂层丝锥
对于强度比较高的材料的攻丝,可采用先钻孔后攻丝的工艺,并适当增大底孔直径,以降低攻丝扭矩和丝锥负荷。东莞TICN丝锥
攻丝前底孔直径的计算是保证螺纹加工质量的关键步骤。底孔直径过大,会导致螺纹牙型不完整,强度降低;底孔直径过小,会增加攻丝扭矩,易导致丝锥折断。底孔直径的计算公式因螺纹类型和材料而异。对于普通螺纹,底孔直径可按以下公式计算:D=d-P,其中 D 为底孔直径,d 为螺纹大径,P 为螺距。此公式适用于塑性材料,如钢、铝合金等。对于脆性材料,如铸铁、黄铜等,底孔直径可适当增大,一般为 D=d-P+(0.05~0.1) P。对于细牙螺纹,底孔直径的计算公式与普通螺纹相同,但需注意细牙螺纹的螺距较小,底孔直径的公差也相应较小。对于英制螺纹,底孔直径可根据螺纹规格查表确定。在实际生产中,还需根据丝锥的类型、加工工艺和材料特性等因素进行适当调整。例如,使用挤压丝锥时,底孔直径应比切削丝锥的底孔直径略大;对于深孔攻丝,底孔直径可适当减小,以补偿攻丝过程中的弹性变形。东莞TICN丝锥
文章来源地址: http://wjgj.jzjcjgsb.chanpin818.com/sdgj/szby/deta_28681056.html
免责声明: 本页面所展现的信息及其他相关推荐信息,均来源于其对应的用户,本网对此不承担任何保证责任。如涉及作品内容、 版权和其他问题,请及时与本网联系,我们将核实后进行删除,本网站对此声明具有最终解释权。